By ERIKA ALLEN
POPULAR local tourist destination Loch Sport’s newest home is defying conventionality and challenging what a house can be.
It’s built like LEGO blocks from three shipping containers and takes eight to 12 weeks to assemble.
Turning the humble shipping container into houses is not a new building solution. The rise of the Tiny House – the #tinyhouse has 3.7 million posts on Instagram – was perhaps the blueprint for shipping container houses. As a movement, Tiny Houses and Tiny Living are touted as economical, and they are a social movement as much as they are architectural.
While single-unit shipping containers service the Tiny House lifestyle, some builders are thinking more ambitiously while still championing the values of Tiny Living – affordability, sustainability, and time efficiency.
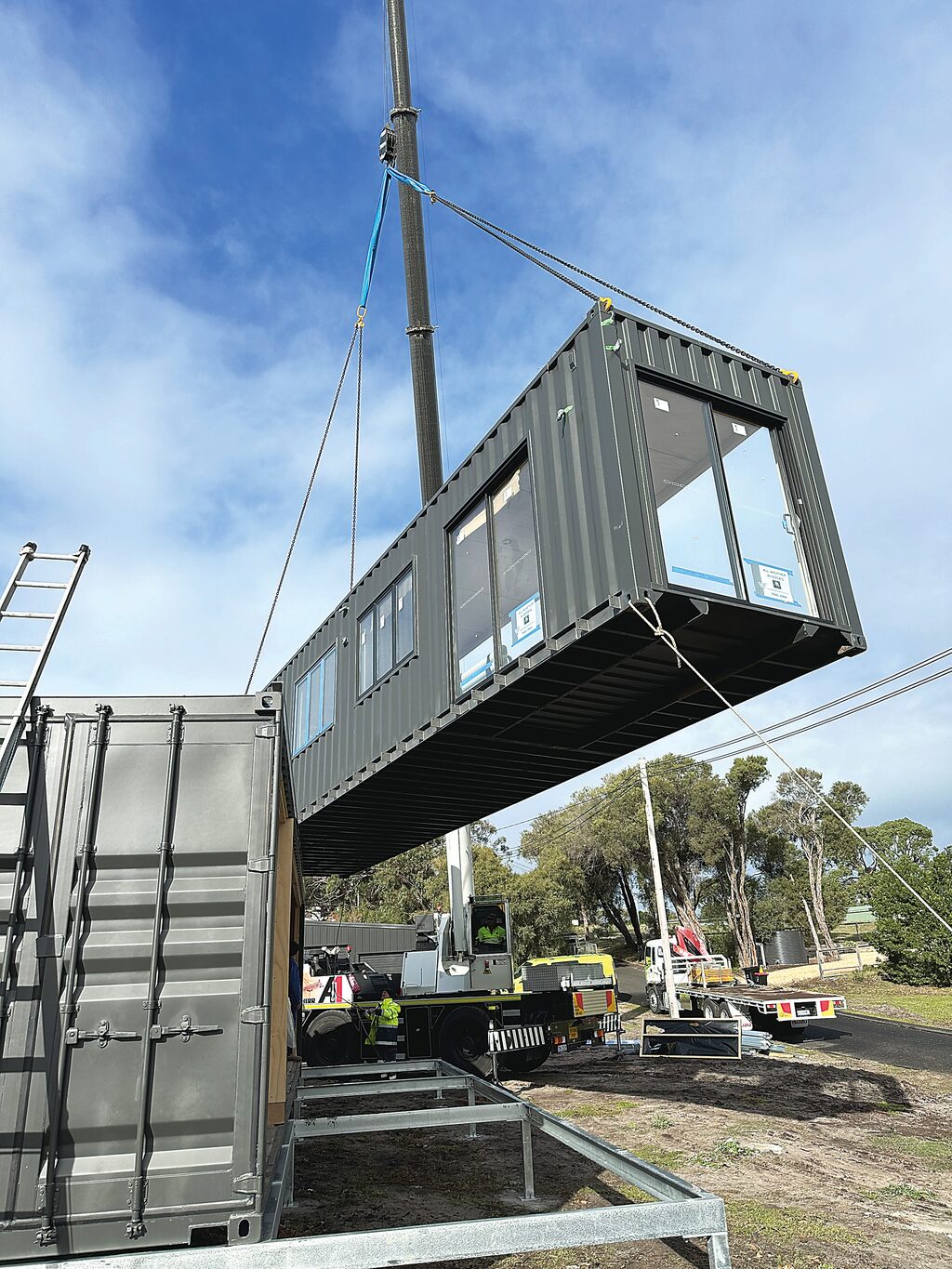
Matt Stubbs is a director of the company Containered, which he started in 2019 after building a holiday home from shipping containers in his home state of Tasmania. He said Containered evolved to “help people get in a home in a quicker manner” rather than waiting up to 12 months for traditional builds.
“Back in 2019, I was actually looking to find a modular solution (to) build on a regional block in Tassie for myself, and I couldn’t find anyone that did that,” he said.
“Modular buildings (are) meant to be an efficient and I suppose quicker and cheaper process, but it seemed like it wasn’t. So, I decided to build my first home as an owner-builder.”
Mr Stubbs said the key to modular homes, which are prefabricated sections or ‘modules’ essentially constructed like LEGO, is their time efficiency.
When the home was complete, Mr Stubbs said more than 20 people came knocking on the door, curious about the project.
The company has built more than 15 modular homes five years later, including one in Loch Sport.
Speedy construction comes to Gippsland
THE swift construction of a three-bedroom, two-bathroom Containered project has recently enthralled Loch Sport locals.
Owners, Matthew and Natalie Kenny from Melbourne bought a block at Loch Sport – their holiday destination – a year ago and commissioned a container house about four months later.
“We wanted something that would look the part, suited our needs that was probably easier for us to look after and maintain, just come in and use it and then just lock it up and leave and we could send friends and family up to use it as well,” Mr Kenny said.
He said the project could have been completed faster but they spent a few months choosing the home they wanted and had to connect services like electricity that weren’t in place already.
“It has probably really taken us eight months from pushing the button and getting everything done,” he said.
He said the block wasn’t connected to electricity, plumbing or sewage like residential blocks are, which would make construction faster.
How fast a house could be constructed was at the forefront of the Kenny’s decision-making.
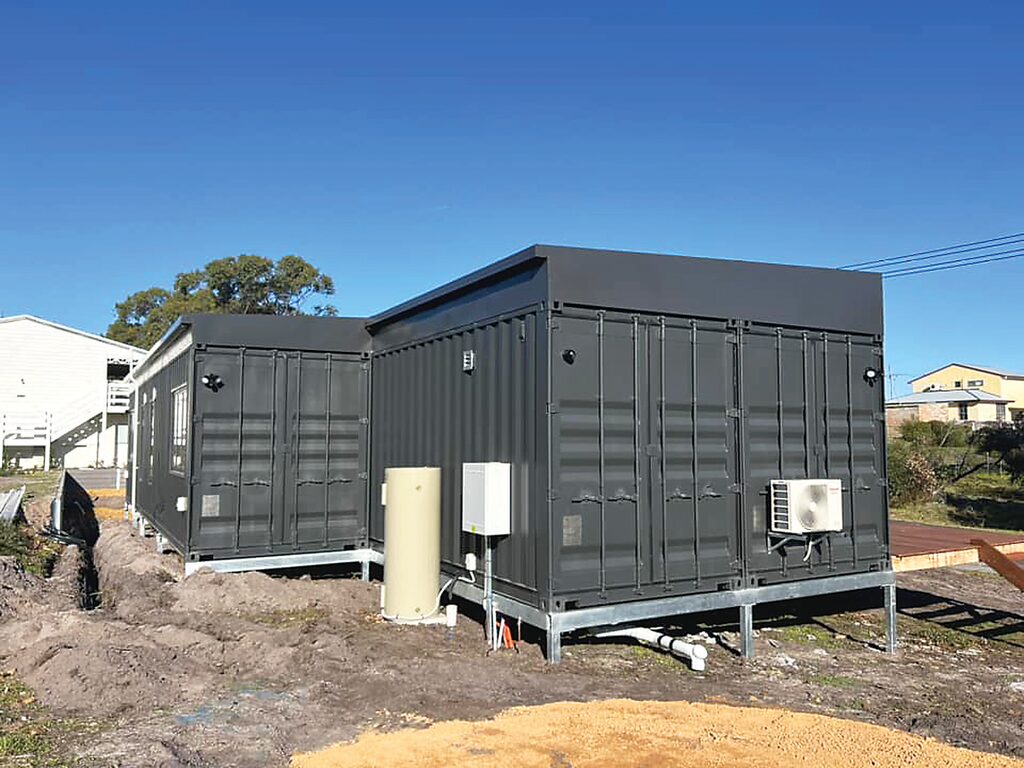
The shipping containers were modified in March and installed on the block four weeks ago. Mr Kenny described the process as “seamless” and was surprised by how quickly they could be assembled.
After shipping containers are sourced (Containered uses single-trip high cube shipping containers from China), Mr Stubbs said it takes about five weeks to prepare the shells and 10 to 12 days to finish the build.
“Containers come in six-metre to 12-metre lengths, they’re 2.4 metres wide and we can configure them any way that the client wants,” Mr Stubbs said.
“The nice thing about it – because the external shell is the structural element – is the internal walls are not there to hold up the roof, so it’s sort of infinite in where we can place walls and divide them up once the containers are joined together.”
Mr Stubbs said the Loch Sport project was loaded onto three semi-trailers and shifted onto a pre-made steel structure using a crane.
“A 40-tonne crane came from Sale and lifted the containers on, and the three containers were bolted together and secured onto the site in the first day of work,” he said.
The project has certainly left an impression on locals.
The Kenny’s admitted to having an appreciation for “things that are a little bit different”.
“It’s not just your bang together (of) containers… once it’s finished, it’s like a real home on the inside,” Mr Kenny said.
He said people walk past saying ‘(It) looks fantastic, just what we needed, something different in the area’. Additionally, they have been sharing updates on the Loch Sport Notice Board Facebook page.
One user commented: “Love the quirkiness of container builds, great to see one getting built here.”
Another said, “Those containers make lovely homes for what I’ve seen.”
Container homes ‘the future’
AS building solutions for working with steel containers have become more accessible, the reality of shipping container homes is not limited to environmental enthusiasts’ intent on recycling, although LEGO fetishists may also be tempted.
Market Watch projected that between 2019 and 2025, the use of shipping containers in houses will have a global compound annual growth rate of 6.5 per cent. In Australia, Facebook groups such as Aussie Shipping Container Homes and Shipping Container Homes Australia have sprung up, serving as wells of shared information and inspiration.
Mr Kenny said container houses could be the “future”.
“The government’s wanting to get houses built for people and the younger generation that are saying ‘how are we gonna pay for all these things?’, it’s a really good way forward for them to maybe (be) able to get a brand-new home that’s cost effective.”
Could this kind of building appeal to a generation of young people disillusioned by overblown, over-mortgaged homes?
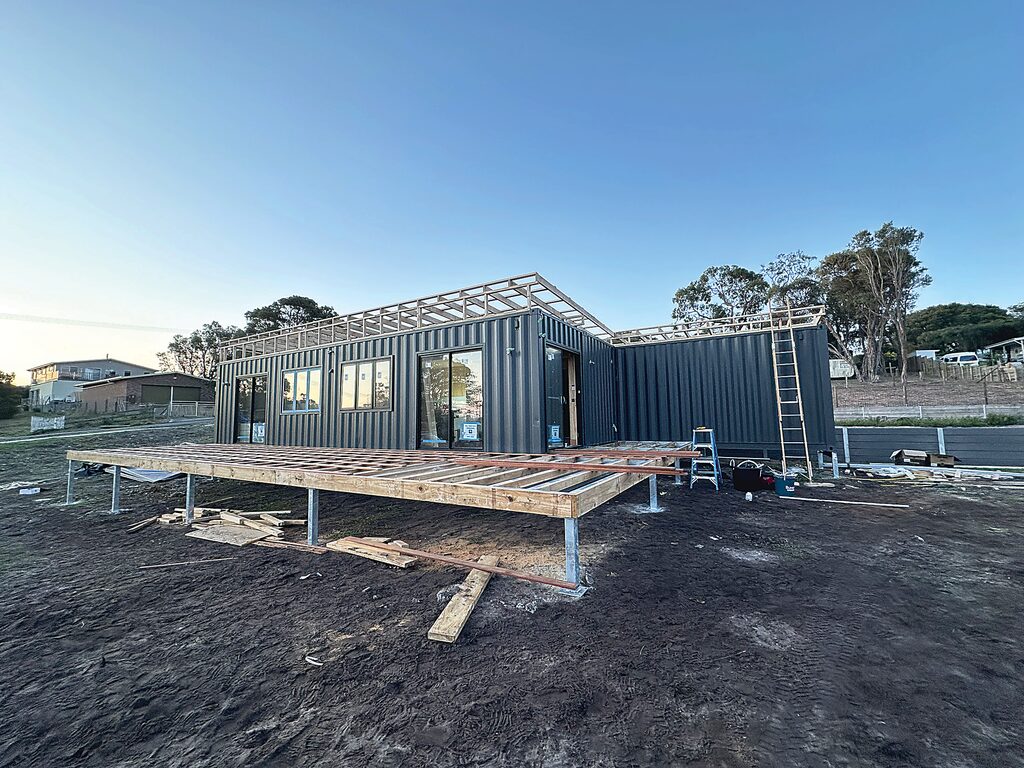
Mr Stubbs said a shipping container home is not necessarily cheaper by the square metre. The Loch Sport project has around 90sqm of internal space.
“But as an overall project, when you’re taking into account the speed of it and the less time that you’re not in a house or the less time you’re paying for a block of land and can’t use it, it generally works out attractively.”
He said people can avoid “double costs,” like renting a temporary house for 12 months.
A standard Containered project – the most popular being the three-bed, two-bath model – costs between $350,000 and $450,000 from start to finish.
“That includes your council permits, transport to the site, the initial building in the factory and then finishing off,” Mr Stubbs said.
On the Loch Sport project, he said: “We’ve used a local electrician, a local plumber, local earthworks, (and) a concreter. So, there’s things that we still engage with at the local level in order to increase efficiency and keep costs down rather than do it all coming out of Melbourne.”
He said the shortened timeframe mitigates the risks of price rises or variations and delays due to shortages of materials.
With little “price fluctuations”, owing to the quick build, Mr Stubbs said the modular solution is good for the client and builder because the risk of not delivering is reduced.
“It’s like getting a quote for a car today and then going to the dealership in two years and expecting to pay the same amount. That’s sort of how traditional building works from a pricing point of view.
“All these things that happen in between those times can affect the final price. There are protections in place for insurers, but the builders then have to honour that initial cost that they quoted so they get stuck, hence why there’s a lot of people building houses that they’re not making money on but they have to finish them.”
The impact of COVID-19 on material costs and labour shortages has dragged out the time to complete projects, pushing up the cost of construction. The first quarterly Cordell Construction Cost Index (CCCI), which tracks the cost of stand-alone house construction, recorded a 0.8 per cent rise.
In April, CoreLogic economist Kaytlin Ezzy said that while growth in national construction costs has continued to ease from the highs seen during the pandemic, price levels remain elevated.
“Current building costs are still 27.6 per cent higher than at the start of the pandemic, which is likely putting significant pressure on builder’s profit margins,” she said.
Rethinking what a house could be
MR Stubbs said the modular solution also gives people a choice, knowing there are alternative ways to build a house.
“Building has occurred the same way for 100 years and not much has changed. The way we sort of look at it, is that just because it’s been done a certain way, that doesn’t mean it’s the best way in the future,” he said.
Instead of manufacturing walls to support a roof, the shipping container shell is the main structural element. Hence, container homes differ from conventional homes in a couple of ways.
“Some people want a big house that is a traditional looking place with bricks and a pitched roof, and then there are a lot of young people that really like the container look. There’s a lot of houses being built that aren’t containers that are clad and dressed up to (capture) the feel of what we’re doing anyway,” Mr Stubbs said.
In fact, you’d have to be quite the shipping container boffin to identify them in some of the elaborate homes they’re being fashioned into.
“Once the roof and everything’s gone on (and) they’re all joined together, you really don’t know apart from looking at one side where the container doors are, you really don’t know it’s containers,” Mr Kenny said about the Loch Sport project.
Mr Stubbs said less space is wasted compared to some traditional homes. The reason is that it can’t afford to be wasted.
The Loch Sport project has three bedrooms, two bathrooms, an ensuite, and a separate toilet and shower with an open living space.
“It’s really the same size as the house I grew up in, you know, in the in the ’80s in Tassie. So, it’s sort of bringing the houses back down a bit in size and making them more efficient, so there’s no hallways in the houses so we don’t waste any space,” Mr Stubbs said.
“I think our clients are really starting to realise that you don’t need two rumpus rooms and a sitting room and a separate dining. You still want (and have the) amenities to still enjoy living in it.”
Mr Kenny said people don’t need “big” houses.
“We’d easily have six people in here any one time, and I think there’s plenty of room for what our needs are.”
In addition to less wasted floor space, Mr Kenny said he’d never seen such a small amount of material waste for a build. He said the project needed one skip bin, and the leftover wood was donated to the local men’s shed.
“I think it’s important we’re not putting back into the garbage system,” he said.
“You’ve got a container that won’t rust, that’ll be here for a long time, so there’d be no need for this to be rebuilt at any point in time.”
Finishing touches are being added to the home, Mr Kenny said, including solar panels and a battery system that will increase its efficiency, like the double-glazed windows and insulation.