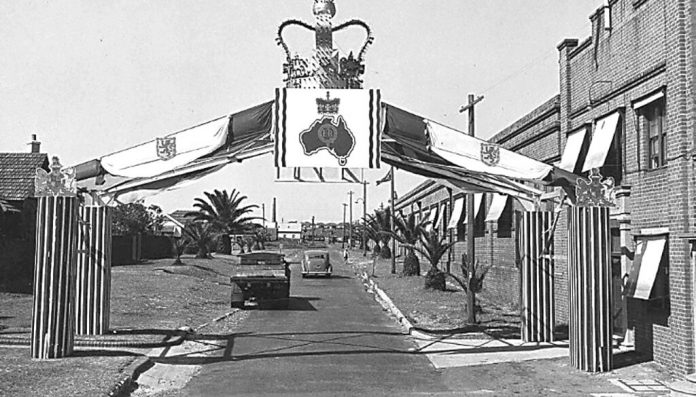
JOHN CAMERON
COMMENT
By JOHN CAMERON THE Maryvale Mill opened in the Latrobe Valley in 1937 and has since grown to be one of the largest employers in the region employing up to 1000 people in direct jobs. Maryvale traditionally manufactures about 600,000 tonnes of paper and board annually from about 1.5 million cubic metres of logs, adding considerable value to the logs unsuitable for sawn timber. The site includes five mills, ECF-free (Elemental Chlorine Free) bleach plant and two wastepaper recycling plants. The opening of the Maryvale Mill in 1937 followed intensive appraisal of surrounding forests and was facilitated by a long-term wood supply agreement to underpin the mill investment. The mill used the waste wood from saw log operations, helped with forest regeneration operations, reduced the bushfire hazard and assisted with a government policy of decentralisation (which over the past few decades has morphed back to ‘centralisation’). The Forests Commission of Victoria wrote in its 1936-37 annual report to both Houses of Parliament: “After intensive field investigations and protracted negotiations between the Commission and Australian Paper Manufacturers Ltd., the largest paper manufacturing corporation in the southern hemisphere, a basis of agreement was reached and the necessary legislation enacted to enable the Company to obtain supplies of pulpwood timber from suitable areas of indigenous hardwood forests”. “From a forestry point of view, the most important feature of this new development is the prospect of the raw material required by the industry being supplied solely from existing and potential sawmill waste, inferior trees and logging slash, and prospective thinnings, all of which timber was formerly discarded as waste due to lack of available markets for such inferior grades of produce”. “The Commission was in the position of being able to guarantee adequate supplies of raw material from these sources for the requirements of the projected plant….all operations of the Company connected with the getting of pulpwood from State forest areas are to be rigidly controlled by the Commission, through the medium of plans of utilization to the provisions of which the Company must adhere”. “The manufacture of wood-pulp is the most important form of wood waste utilisation, and the advent of this industry should prove of immense economic value to the State” (and it was). “Regeneration operations will be facilitated by the removal of the bulk of the discarded timber from sawmilling areas and the fire hazard will similarly be decreased”. “The successful inauguration of the new undertaking will be an important advance in the rural economy of the State. A large body of labour will be permanently employed both in the forest and in the mill, and the fact that the industry will have its headquarters in a country centre will be of material assistance in promoting a policy of decentralization of both industry and population”. This original pulpwood agreement underpinned a substantial investment in the Latrobe Valley that created thousands of jobs and considerable regional development over 85 years. The actions 85 years ago provide a case study on how a government focused on supply-side economics can create wealth and prosperity for regional Victoria. APM saw an opportunity to reduce reliance on the supply of expensive imported pulp but needed long-term security of resource supply to justify its substantial investment in a new pulp mill at Maryvale. The Dunston Country Party Government saw the potential for a new industry to deliver decentralisation, jobs and prosperity and committed to supply the wood, along with supporting the supply of essential transport, water and power for the new mill. Prior to the Maryvale mill, Australian papermaking was undertaken at Southbank Melbourne (from 1868), Barwon near Geelong (1878), Broadford (1890) and Sydney (from 1890), using rag and waste paper as fibre. High international freight costs precluded the use of imported wood pulp. At that time the world’s pulping industry was based on the long-fibred softwoods from native forests of Europe and North America. The use of short fibre Eucalypt pulp made at Maryvale to replace imported long fibred pulp represented a major technological breakthrough at the time. Kraft pulping of Mountain Ash (Eucalypt regnans) produced pulp that was easy to bleach for white papers and newsprint. Wood procurement for Maryvale began in 1938 when pulp production was about 90 tonnes per day or 31,000 tonnes per year and pilot paper production began. Over 85 years, Maryvale’s pulp production grew to about 600,000 tonnes per year. In 1937-38 the Forests Commission supplied Maryvale with 1662 cunits (or 166,200 cubic feet) equivalent to 4706 m3 of Eucalypt pulpwood, along with input from many other sources, including settlers. In 1939, one of Victoria’s worst bushfires burnt most of the Ash forest resource that was to supply the pulpwood for the new mill at Maryvale. Australian Paper Manufactures Ltd, commonly known as APM, had a strong research capability and tests showed that pulp could successfully be made from salvaged fire-killed Ash and mixed species Eucalypts from the foothills. Large quantities of fire-killed Ash were pulped at Maryvale through the 1940s and early 1950s. I recall the odd load delivered in 1972 when I joined APM’s wholly owned forest subsidiary called APM Forests (later renamed Australian Paper Plantations). Maryvale input was about 28,000 m3 in 1939. Over the 85 years Maryvale’s log input has grown to over 1.5 million cubic metres per year with about half Eucalypt and half pine pulpwood. M1 paper machine began operation in 1940. M1 was followed later by M2 and M3 paper machines and M3 was later converted to produce white papers. In 1987 M4 machine was built for the production of liner board for cardboard boxes and in the 1990s M5 was built for the production of white papers including the iconic Reflex copy paper. In 1985 a new 160,000 tonne per year continuous digester pine kraft mill was commissioned and fed with the thinnings and lower grade clear-fall logs from the maturing pine plantations previously established by APM Forests and the Forests Commission on farmland that was marginal for farming. In 1986, APM was renamed Amcor, who decided to focus on packaging. In the 1990s Amcor sold its Morwell sawmilling business called Brown and Dureau and in 2000, spun off into a new company called Paperlinx, its papermaking (Australian Paper) and forestry business (Australian Paper Plantations known as AP Plantations) in the region. Paperlinx sold Australian Paper Plantations to Hancock Victorian Plantations in 2001 and sold its pulp and paper manufacturing including Maryvale to Nippon Paper in 2009. Paperlinx then ‘burnt’ the proceeds on its failed attempt to become an international paper merchant (old world business). The demerging of the forests, sawmill and pulp/paper operations into separate ownership substantially reduced economies of scope, synergies and wood quality benefits previously generated by the three operations under common Amcor ownership. This aspect of the divestments contributed to the eventual closure of the softwood sawmill at Morwell and increased pulping costs at Maryvale. In 2007, Paperlinx invested about $203 million in upgrading bleached eucalypt pulp production by 90,000 tonnes per year, requiring plantation supply to be augmented by ongoing native Eucalypt supply under a long term supply agreement with the Victorian government; recent events suggest sovereign risk under government contracts has morphed from low risk to as risky as junk bonds. In 2015 Nippon then invested about $90 million in a waste paper recycling plant to annually convert 80,000 tonnes of recovered fibre into 50,000 tonnes of deinked pulp. Australian Paper was later renamed Ópal. Australian Paper Maryvale looks like it now has to abandon two investments totalling about $300 million, plus possibly much of the investment in M5, along with investment in supporting infrastructure and the training of around 220 experienced operators. The loss of 220 jobs at the mill, coupled with job losses by harvesting and maintenance contractors, could not come at a worse time for the Latrobe Valley, where unemployment is the highest and population growth rate the lowest of comparable Victorian regions. The government’s transitional assistance, following the closure of Morwell and Hazelwood mines and power generation, has failed. The Latrobe Valley is already disadvantaged by a reckless rather than well-planned transition to renewables based on more imported components rather than assisting local manufacture; a failed forestry plan that has delivered a 50,000 ha decline in plantation area over the past five years, and a ‘Safer Together’ bushfire policy that is likely to deliver ‘Scorched Together’, unless someone in Spring Street wakes up to the fact that the government’s 70% residual risk bushfire target is only achieved with considerable wildfire, and 70 per cent residual risk roughly equates to only ’30 per cent safe’. Another drought year like 1898, 1926, 1944, 1968 and 1983 and the plantation resource that is now Maryvale’s mainstay is threatened with substantial fire losses. These drought years were worse than 1939 when the 1939 bushfire almost reached Maryvale. Maryvale’s sustainable future requires effective government support to protect and enhance its supply chain. References: Annual reports of Forests Commission of Victoria, annual reports and announcements of APM and successors Amcor and Paperlinx and R McCarthy (2019 and updated 2021) APM Forests – Timeline. John Cameron (Dip Hort Burnley and MBA Monash) is a Traralgon business consultant who previously worked at APM Forests, Amcor and AP Plantations.